Fibre Processing
There are many steps involved in taking raw fibre form the shearing floor to the finished product of purchasable and useable alpaca fleece.
Shearing
Shearing takes place annually, usually in spring. Alpacas are shorn once a year, usually in spring. Shearing is the biggest maintenance required and usually takes around five to ten minutes per animal for an experienced alpaca shearer. Alpacas don’t have a flexible backbone so they cannot be shorn the same way as sheep. The preferred method of shearing is to lay the animals on their side, either on a shearing table or the ground, and restrain their legs with a tether at each end to protect both the shearer and the alpaca. Electric sheep-shearing equipment is normally used, but because alpaca fibre is non-greasy, care needs to be taken that shears do not over-heat. Depending on fineness and density, alpacas will cut between 2.5 and 5 kg of fleece.
If you are purchasing your first alpacas, ask the vendors for the name of a recommended shearer, or ask if you can bring the alpacas back to the property on their shearing day.
Pre-classing
Alpaca fleece is skirted prior to sending to the classer to remove vegetable matter or unusable fibre. This operation saves the classer time and will increase the financial return to the grower.
Classing
As with all natural fibres, alpaca needs to be sorted to meet the needs of processors. The main properties are fibre diameter (micron), length and colour.
Scouring
All natural fibres need to be scoured or washed to remove dirt and grease frm the fleece. Alpaca has a low grease content and will yield around 90% of initial fleece weight after scouring.
Carding
Once the fleece is scoured , the individual fibres need to be aligned. This process will also remove some of the unwanted vegetable matter
Top making
The fibres go through a finishing alignment called gilling before being combed into a product known as a top. This top has the appearance of a loose rope without the twist.
Spinning
Tops are fed into spinning machines to make a yarn for either knitting or weaving. This is the last process in the chain before the fabric is manufactured.
Dyeing
An advantage of alpaca is that the lighter colours are easily dyed to suit contemporary fashion. The beautiful natural colours of alpaca are manufactured directly into top end products.
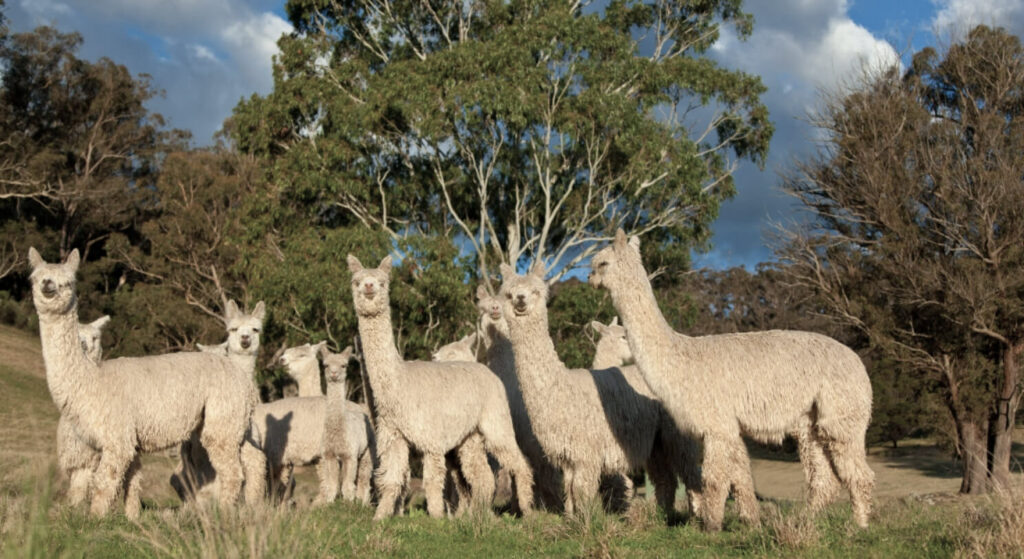
Understanding fleece results
Testing and then understanding fleece testing results is invaluable to alpaca breeders. It allows stud owners to make educated and informed decisions in their breeding programs. It also gives breeders information on the quality of their fleece in regards to processing into products.
Useful Resources
- Alpaca Fibre Classing video
- Shearer business directory
- AWEX Classers
- Fleece buyers and processors directory
The AAA has shearing and classing resources available in the shop